Description
Running video of 12MM wedge anchor clip sheet metal Progressive stamping die
12MM wedge anchor clip sheet metal Progressive stamping die
Line | Description | Parameters |
---|---|---|
1 | Design: | As per standard wedge anchor clips design, customer design and specific requirements |
2 | Accept drawing format: | .pdf/.jpg / .dwg / .igs / .stp etc.. |
3 | Material: | carbon steel, alloy steel, stainless steel, high-speed steel and etc. |
4 | Size: | Accordng to the drawings or Customized drawing |
5 | Material standard: | If there is no any specially requirement, we often sugguest our customer to try the equivalent China National (GB) standard material that our engineering team proposes which to be properly converted from ANSI, ASTM, SAE, EN, DIN, BS, JIS, and etc., to contribute the material cost control. If it is necessary to use exact designated material no., it is also possible choice. |
6 | Components and types: | sheet metal high speed Progressive stamping die,blanking die,trimming die,punching die,flanging die,bending die, drawing die and etc. |
7 | Fuctions and usage: | -blanking-piercing-cutting off-trimming-stretching-deep drawing-flanging-bending-plunge-bulging-finishing |
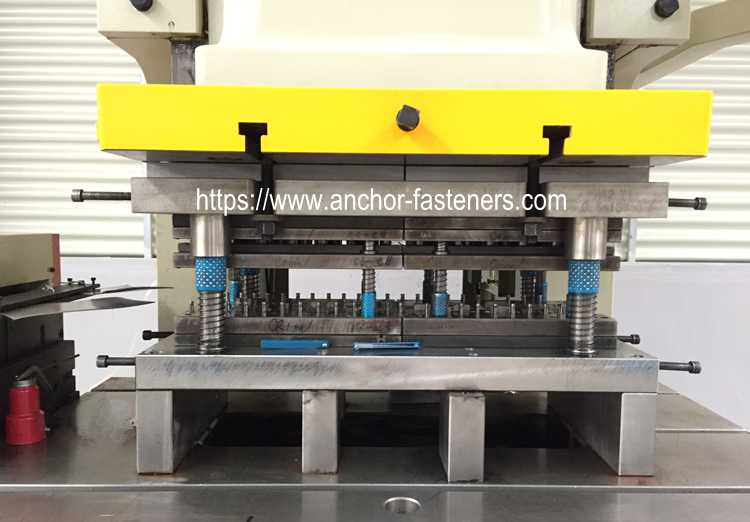
wedge anchor clip sheet metal Progressive stamping die
Progressive Die Stamping
Progressive die stamping is a metal forming process widely used to produce parts for various industries, such as automotive, electronics and appliances. Progressive die stamping consists of several individual work stations, each of which performs one or more different operations on the part. The part is carried from station to station by the stock strip and is cut out of the strip in the final operation.In progressive die stamping, a steel strip is formed into a finished part in several operations.
The decision to produce a part in progressive die or transfer die is dependent on size, complexity and volume of production. Progressive die stamping is used to produce a large number of parts and keep the costs as low as possible. The highest demands in precision and durability must be met.
Due to the complexity of progressive dies, it is important to address all the factors that contribute to achieving the desired level of part quality, including blank position, pilots, blank boundary and stretch-web deformation.
Pilots play an important role in progressive die stamping – they fix the strip into an appropriate position and maintain control over it. In addition, they are essential for precise sheet positioning during tool closing and drawing operations in transfer dies. Other factors to be considered are timing and interaction of carriers, pads, and upper and lower tools. The benefits of progressive die stamping are increased productivity and significant cost reduction for high-volume production.

wedge anchor clip sheet metal Progressive stamping die details
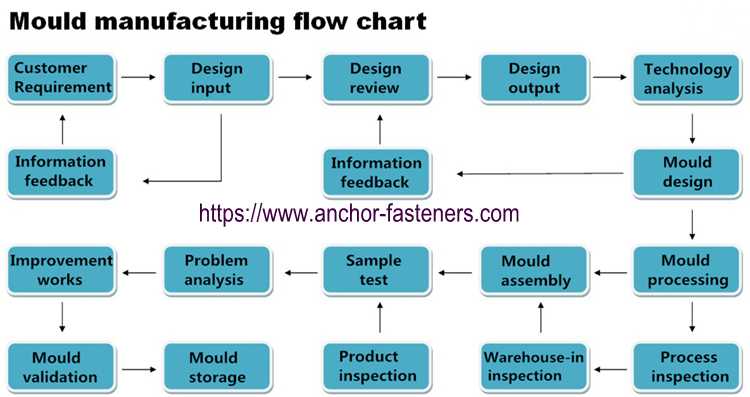
wedge anchor clip sheet metal Progressive stamping die making process
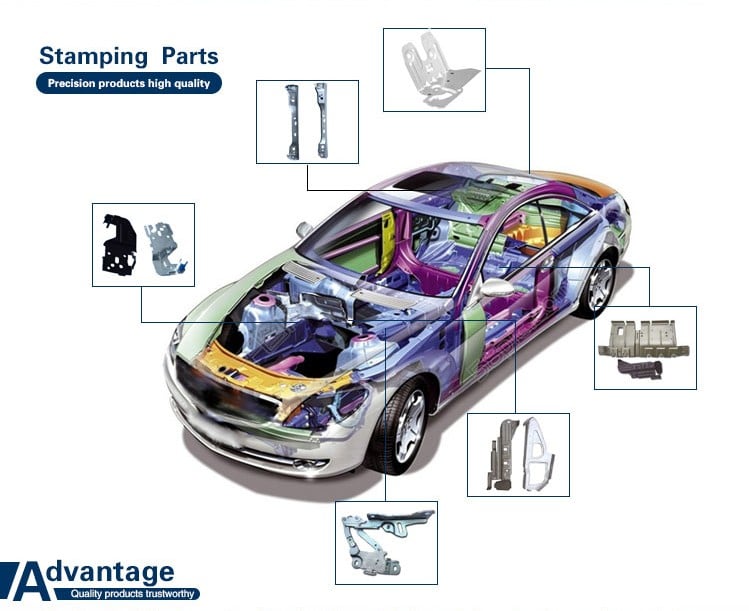
sheet metal Progressive stamping die stamping automotive parts
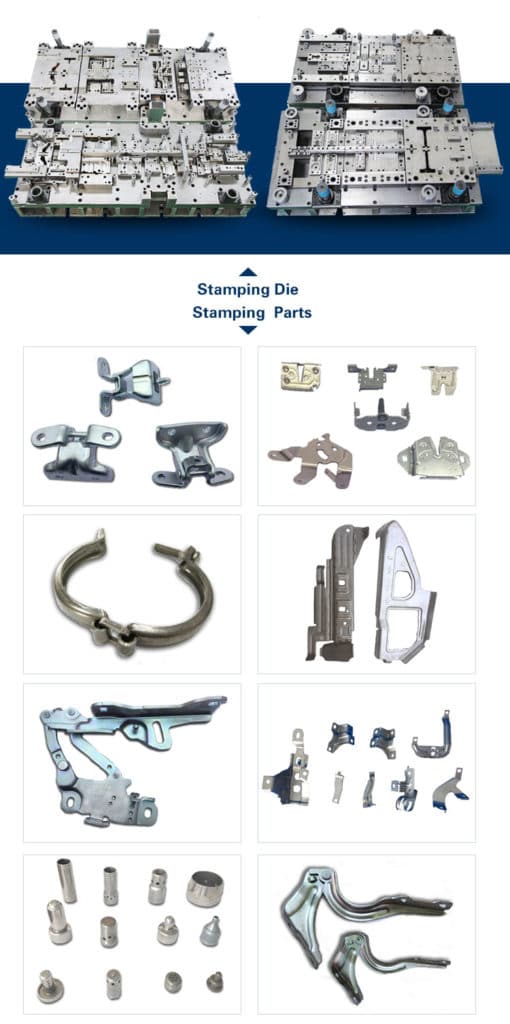
sheet metal Progressive stamping die and stamping auto motive part
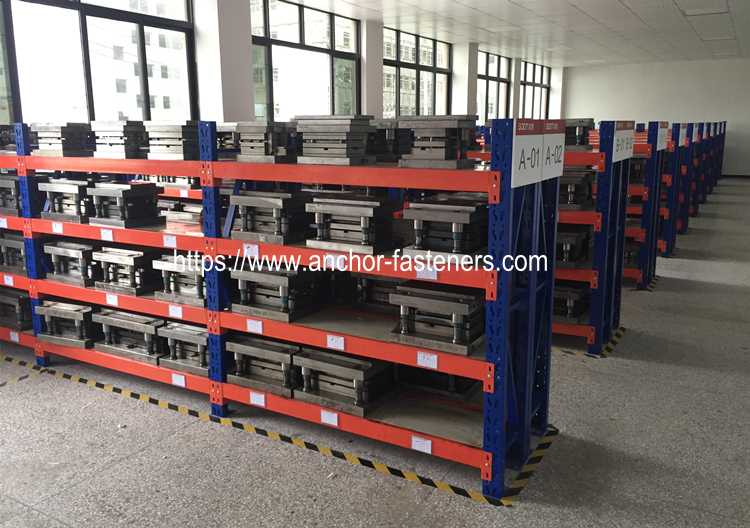
wedge anchor clip sheet metal Progressive stamping die storage
PROGRESSIVE DIE VS. TRANSFER DIE STAMPING
The two types of die stamping processes you may encounter are progressive die stamping and transfer die stamping. What do these different types of stamping entail, and what are the advantages and disadvantages of each? What types of applications are most common to transfer die vs. progressive die stamping and vice versa?
WHAT IS PROGRESSIVE DIE STAMPING?
In progressive die stamping, a coil of metal is fed through a machine that consists of a series of stamping stations that perform simultaneous operations. The metal strip moves through the drawing process, with each progressive die station altering the configuration on the metal from the previous station. Once the metal has gone through the entire machine and all the stamping stations, the piece will be complete.
WHAT ARE THE ADVANTAGES OF PROGRESSIVE DIE STAMPING?
Progressive die stamping is well-suited to operations needing to produce many small pieces quickly, since you can perform multiple cutting and forming operations simultaneously. This combining of operations can also save on costs, although you will have to pay for permanent tool steel die sets. Progressive die stamping can also allow you to maintain close tolerances if you have the right tools.
WHAT APPLICATIONS TYPICALLY USE PROGRESSIVE DIE STAMPING?
You can find progressive die stamping in a variety of industries, including automotive, locomotive, heavy trucks and RVs, medical, electronics and agriculture.
WHAT IS TRANSFER DIE STAMPING?
In transfer die stamping, rather than feed the metal part through a series of stations, a mechanical transport system transfers the part from station to station. The transfer die can be a single die or part of several dies lined up in a row. Transfer die stamping is used to perform operations on the part free from the strip.
WHAT ARE THE ADVANTAGES OF TRANSFER DIE STAMPING?
Transfer die stamping tends to be more economical than progressive die stamping. It is also much more versatile than progressive die stamping. If your part has features like cut-outs, pierced holes, ribs, knurls or threading, you can use transfer die stamping to work these into regular press operations so that you don’t need secondary operations at added cost.
WHAT APPLICATIONS TYPICALLY USE TRANSFER DIE STAMPING?
You will use transfer die stamping when you have large parts you need to transfer between multiple presses to complete them, such as shells, tube applications, frames and structural components. You can find transfer die stamping in all the industries where you find progressive die stamping. It all depends on the specific type of part you are stamping and your requirements for that part.