Description
M16 Stainless steel heavy duty shield anchor caps pressing tooling
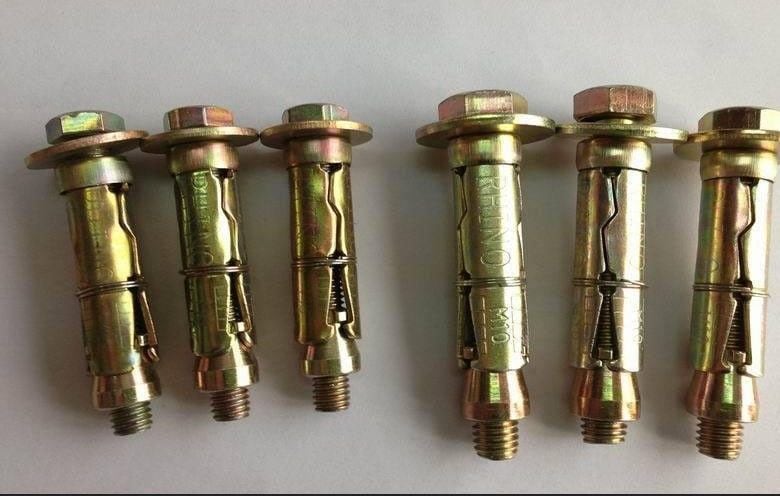
Clips made by shield anchor bolt clips making machine
6MM wedge anchor clip sheet metal Progressive pressing die
Line | Description | Parameters |
---|---|---|
1 | Design: | As per standard wedge anchor clips design, customer design and specific requirements |
2 | Accept drawing format: | .pdf/.jpg / .dwg / .igs / .stp etc.. |
3 | Material: | carbon steel, alloy steel, stainless steel, high-speed steel and etc. |
4 | Size: | Accordng to the drawings or Customized drawing |
5 | Material standard: | If there is no any specially requirement, we often sugguest our customer to try the equivalent China National (GB) standard material that our engineering team proposes which to be properly converted from ANSI, ASTM, SAE, EN, DIN, BS, JIS, and etc., to contribute the material cost control. If it is necessary to use exact designated material no., it is also possible choice. |
6 | Components and types: | sheet metal high speed Progressive stamping die,blanking die,trimming die,punching die,flanging die,bending die, drawing die and etc. |
7 | Fuctions and usage: | -blanking-piercing-cutting off-trimming-stretching-deep drawing-flanging-bending-plunge-bulging-finishing |
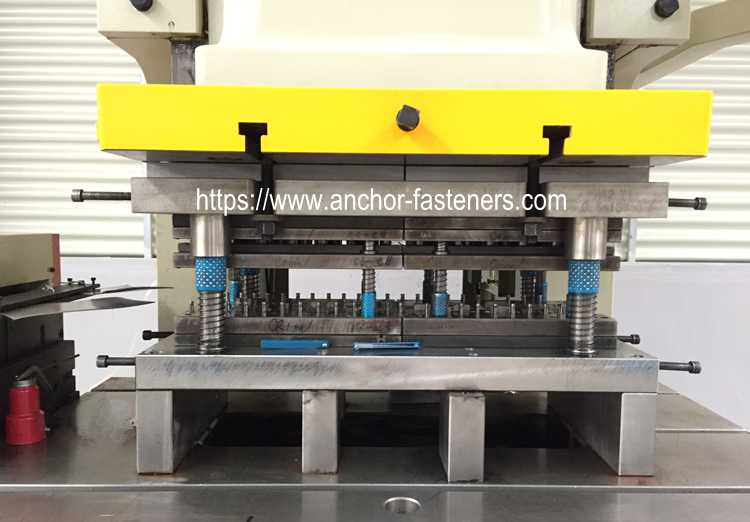
wedge anchor clip sheet metal Progressive stamping die
Many traditional power press metal stamping companies can perform one only one action: single stroke, short-run stamping.
This process requires one tool for each operation needed to make a finished part,meaning long lead times, high labor costs, and an inability to create intricate or tight-tolerance parts.
Luckily there is a stamping process called progressive stamping, which ESI has been using to perfection for more than two decades.
Traditionally, fabricating parts that required more than a bend or two was costly and inefficient.
A manufacturer could either repeatedly change the tool on a single press or occupy a number of presses, each performing one action required for a completed part. Even using multiple presses, secondary machining services were often required to truly complete a part.
The Benefits of High Volume Progressive Stamping
With progressive metal stamping, ESI eliminates those hassles and inefficiencies. A progressive stamping tool features a number of stations, each with a unique function.
As strip metal feeds through a progressive stamping press, unrolling steadily from a coil, each station in the tool performs a different cut, punch, or bend.
The actions of each successive station add onto the work of the previous stations, resulting in a completed part.
For very simple parts, progressive die metal stamping may not be the best option. But there are many scenarios in which progressive stamping is ideal. Advantages of progressive stamping include:
Speed: With a continual feed of material, progressive stamping machines operate at extremely high speeds of hundreds of parts per minute and with minimal downtime.
- Low Labor Cost: One operator can oversee many machines that run unattended due to electronic monitoring embedded in our custom tooling.
- Run Length: The same continual feed of material that provides progressive stamping it’s speed also allows for long production runs. More production time between material changes means more completed parts in shorter amounts of time.
- Minimal Scrap: Scrap metal is inevitable in any manufacturing process, but it is minimized by optimized tool design of progressive stamping.
- Quick Setup: Multiple setups, tool changes, and die changes are required to produce complex parts with conventional short-run stamping methods; only one setup is required to produce completed parts using progressive stamping.
- Complex Geometry: Creation of parts with complex geometries is possible by the building nature of the die stations in a progressive tool.
- High Repeatability: The dies of a progressive stamper are hard tooled. They can withstand the high volume runs of progressive stamping without degrading, maintaining the high quality of the parts produced.
- Low Part Cost: These factors combine to reduce the per part cost of parts manufactured by progressive stamping.

wedge anchor clip sheet metal Progressive stamping die details
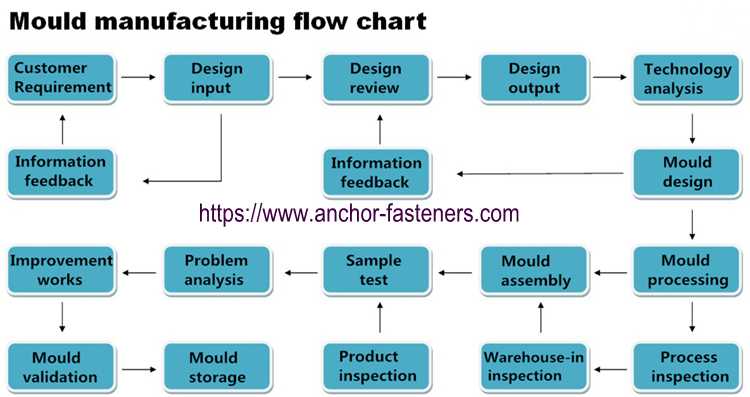
wedge anchor clip sheet metal Progressive stamping die making process
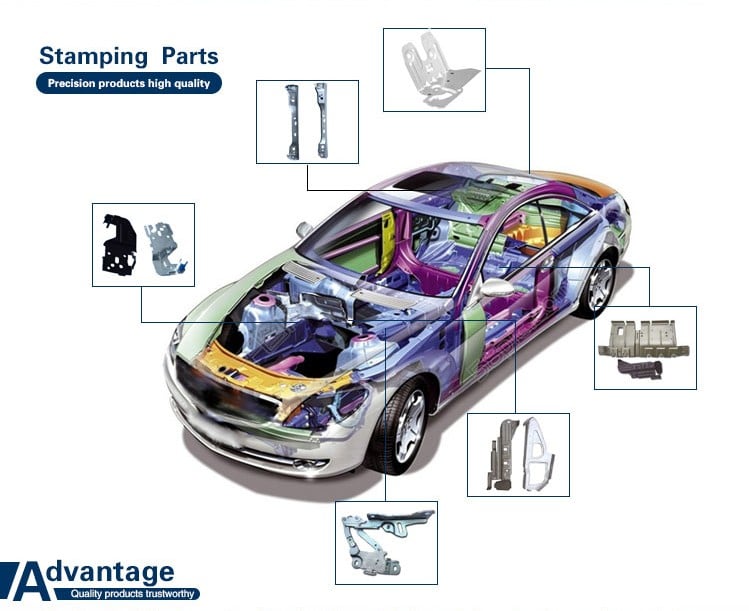
sheet metal Progressive stamping die stamping automotive parts
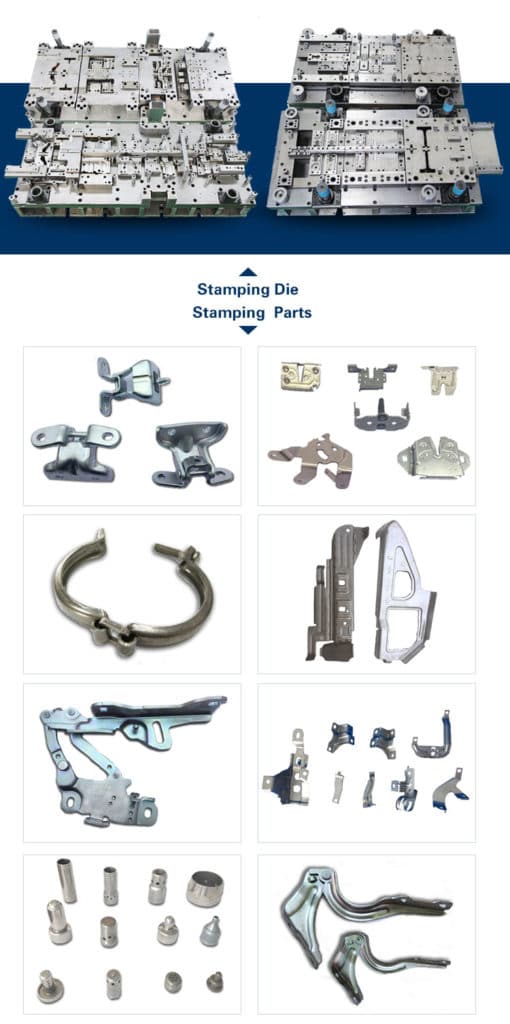
sheet metal Progressive stamping die and stamping auto motive part
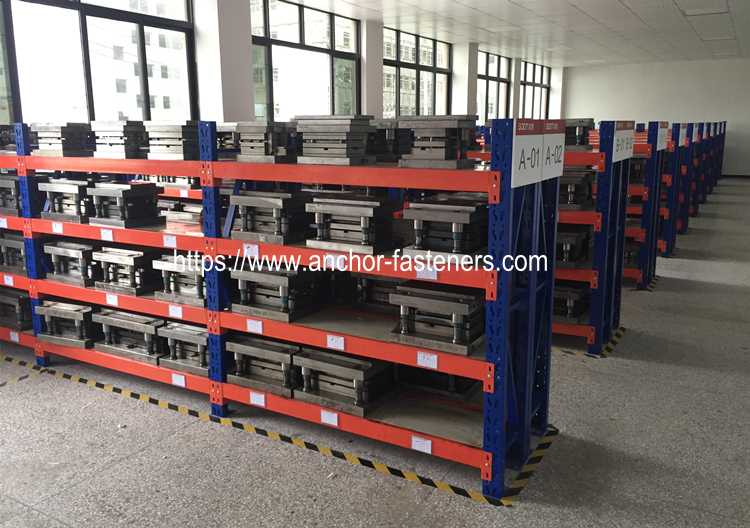
wedge anchor clip sheet metal Progressive stamping die storage
PROGRESSIVE DIE VS. TRANSFER DIE STAMPING
The two types of die stamping processes you may encounter are progressive die stamping and transfer die stamping. What do these different types of stamping entail, and what are the advantages and disadvantages of each? What types of applications are most common to transfer die vs. progressive die stamping and vice versa?
WHAT’S PROGRESSIVE DIE STAMPING?
In progressive die stamping, a coil of metal is fed through a machine that consists of a series of stamping stations that perform simultaneous operations. The metal strip moves through the drawing process, with each progressive die station altering the configuration on the metal from the previous station. Once the metal has gone through the entire machine and all the stamping stations, the piece will be complete.
WHAT ARE THE ADVANTAGES OF PROGRESSIVE DIE STAMPING?
Progressive die stamping is well-suited to operations needing to produce many small pieces quickly, since you can perform multiple cutting and forming operations simultaneously. This combining of operations can also save on costs, although you will have to pay for permanent tool steel die sets. Progressive die stamping can also allow you to maintain close tolerances if you have the right tools.
WHAT APPLICATIONS TYPICALLY USE PROGRESSIVE DIE STAMPING?
You can find progressive die stamping in a variety of industries, including automotive, locomotive, heavy trucks and RVs, medical, electronics and agriculture.
WHAT IS TRANSFER DIE STAMPING?
In transfer die stamping, rather than feed the metal part through a series of stations, a mechanical transport system transfers the part from station to station. The transfer die can be a single die or part of several dies lined up in a row. Transfer die stamping is used to perform operations on the part free from the strip.
WHAT ARE THE ADVANTAGES OF TRANSFER DIE STAMPING?
Transfer die stamping tends to be more economical than progressive die stamping. It is also much more versatile than progressive die stamping. If your part has features like cut-outs, pierced holes, ribs, knurls or threading, you can use transfer die stamping to work these into regular press operations so that you don’t need secondary operations at added cost.
WHAT APPLICATIONS TYPICALLY USE TRANSFER DIE STAMPING?
You will use transfer die stamping when you have large parts you need to transfer between multiple presses to complete them, such as shells, tube applications, frames and structural components. You can find transfer die stamping in all the industries where you find progressive die stamping. It all depends on the specific type of part you are stamping and your requirements for that part.