Description
Specifications of Closed hydraulic CNC turret punch
System Features
1. With the graphics function required for punching, nibbling function.
2. Simple international G code programming, easy to operate and use.
3. The internationally accepted RS232 standard interface facilitates communication with a computer.
4. Configure advanced all-digital AC servo motor and servo system.
5. Color display.
6. Pulse encoder semi-closed loop feedback.
7. Field programming, background programming.
8. Chinese display.
9. Has a graphical simulation function.
10 Convenient backup of system parameters, ladder diagrams and machining programs, and online processing of large-capacity machining programs.
11. Interpolation, position detection and servo control in nanometers enable high-speed and high-precision machining.
12. Use ultra-high speed serial data bus with few wiring cables.
13. High degree of integration, using dedicated software. The startup time is short, and the data is suddenly lost when the power is turned off suddenly.
System function
1. Linear axis: X Y axis, turret axis: T axis.
2. There are alarm displays for many mechanical and electrical faults such as overtravel.
3. With self-diagnosis function.
4. With soft limit function.
5. International general G code programming.
6. With mold compensation function.
7. With pitch compensation.
8. With backlash compensation.
9. Has a coordinate offset function.
10. With relocation function.
11. With automatic, manual and semi-automatic operation modes.
12. With clamp protection.
13. With parameter programming function.
14. With fast positioning and stamping lock function.
Serial number | name | parameter | unit | Remarks |
1 | Punching force | 300(30)/ 500(50)/800(80) | KN(T) | |
2 | Rack structure | “O” type closed rack | electric furnace tempering treated | |
3 | Maximum processing sheet size | X axis 2500 | Mm | Secondary positioning can process 5000mm |
Y axis 1250 | Mm | |||
4 | Processing maximum sheet thickness | 4 | Mm | |
5 | Maximum diameter of one punch | Φ88.9 | Mm | Non-standard can be customized. |
6 | Highest punching frequency | 280 | Times/minute | |
7 | Repositioning cylinder | 2 | set | |
8 | Control axis number | 3/4 (X, Y, T, Z) | One | Rotating station Optional |
9 | Mold form | Long guide 85 series international standard mold | ||
10 | Mold processing life | 500000 | Times | |
11 | Turret station distribution | A, B, C, D | Standard | Non-standard can be customized. |
12 | Workbench structure | Seamless Brush / universal steel ball table | Stainless steel edging | |
13 | Maximum feed speed | X axis 80 | m/min | |
Y axis 80 | m/min | |||
14 | Max. Turret speed | 40 | Rpm | |
15 | Punching precision | ±0.1 | Mm | |
16 | Maximum load weight | 150 | Kg | |
17 | Total power | 21 | KW | |
18 | Air pressure | 0.55 | MPa | |
19 | power supply | 380±5% | V | or customized |
20 | Dimensions | Length × width × height 5000 × 5000 × 2100 | Mm | |
21 | Total Weight | 12 | T |
Features of Closed hydraulic CNC turret punch
(1) Roulette:
1. The turret wheel disc is tempered and tempered by 45# carbon steel; the special tooling is used for pair processing, which ensures the coaxiality of the upper and lower mold positions and prolongs the positioning accuracy of the mold; The wheel-type structure, while reducing the gravity of the mold wheel itself, still maintains a long guiding structure, which ensures the guiding stability of the mold.
2. The company is equipped with a large-scale imported (Swedish Hexagon) three-coordinate measuring instrument. The wheel is assembled after passing the test (the indexing hole indexing value cannot be detected by other measuring tools).
(2) Rotating station (rotary station):
adopting worm and worm transmission mode, the transmission precision is high; the rotating station is composed of turbine, worm, transmission shaft, synchronous gear, gear box and other components, and is installed in the synchronous gear box. The servo motor is connected in a straight line, the synchronization is reliable, the transmission precision is high, the concentricity and the same position of the upper and lower cutters of the self-rotating mold are ensured; the rolling rotary device of the upper and lower mold sleeves of the self-rotating mold reduces the friction coefficient, and the limit is large. Reduces wear and extends the life of the self-rotating mold. The existing traditional rotating mold sleeve is driven by synchronous belt, the transmission link is too much, the transmission mode is complicated, the transmission distance is long, the processing and installation process is cumbersome, so that after the self-rotating mold manufacturing and installation is completed, the accumulated error is too large, and it is difficult to accurately control. The same position of the upper and lower self-rotating mold tools, so that the mold is seriously damaged during the punching process, the use cost is too high, and the thin plate cannot be punched.
(3) The internationally equipped pneumatic components ensure the reliability of the performance of the whole machine.
(4) Adopting imported large lead ball screw and linear guide,
(5) The use of universal ball and brush plate hybrid work surface not only reduces the noise and vibration of the machine tool, but also has a good protection effect on the surface of the processed plate, which can effectively prevent the surface of the plate from being scratched; The unique work surface dust-proof design structure can prevent the collision of the board caused by the excessive clearance, and at the same time play the dustproof effect on the guide rail and the screw rod; effectively prevent the dust and iron filings from falling onto the guide rail and the screw rod. The surface causes the ball to wear, effectively extending the service life of the guide rail and the screw; the periphery of the table and some of the countertops are protected by stainless steel, which is elegant, durable and durable. The data line protection towline is changed from the traditional way to the side of the fuselage to reduce the gap between the worktable and prevent the scraper and the striker. The assembly of the guide rail and the screw rod are all corrected by the laser collimator to ensure the straightness and parallelism of each guide rail and screw.
(6) Using “O” type (closed) steel plate to weld the fuselage, after high temperature tempering treatment, completely eliminate the internal stress removal caused by welding and avoid deformation of the fuselage; the feeding bracket adopts a clamping process to avoid the cause The feeding speed is too unstable due to excessive parallelism and flatness tolerance caused by repeated positioning of the secondary clamping, and the guide rail slider and the screw nut ball are damaged; the adjusting bolt is arranged outside the feeding bracket, so that the feeding tray has a fine adjustment function. It solves the drawback that the natural deformation caused by the use of the age is not adjustable.
(7) Welding parts and castings are tempered to eliminate internal stress; all machined parts are processed in the company (all precision parts are completed by the machining center), assembled after passing the test, and effectively controlled. The machining accuracy of each component eliminates the accumulated tolerances generated during assembly of the assembly.
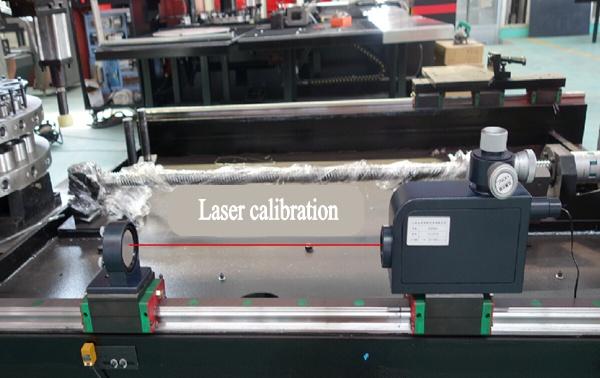
Laser calibration
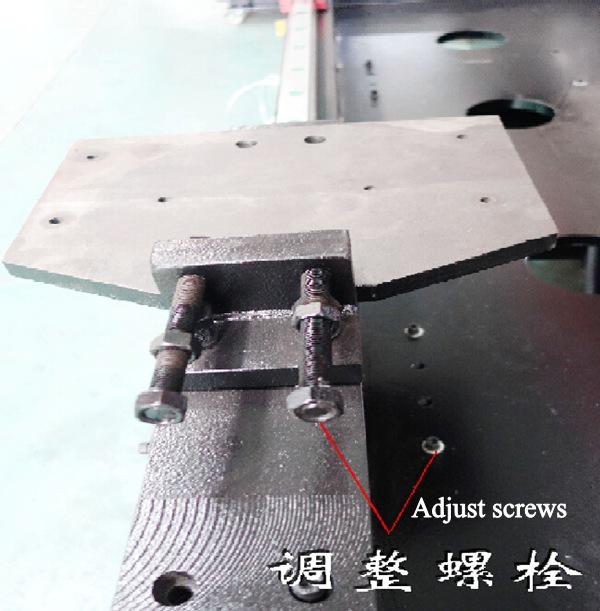
Adjust screws
(8) Using floating pneumatic clamps, the clamping force is large and the feeding is stable; the integral dovetail type carriage has good rigidity and convenient movement of the clamps. The beam adopts double rail design, and the feeding is stable and the positioning is accurate.
(9) The system has automatic clamp protection function, which can not be punched in the protection area, only for displacement movement, to ensure the continuity of the program operation.
(10) Adopting the Nanjing (Elfa) hydraulic station of a well-known domestic listed company. The main components of the stamping system of the hydraulic station are imported products (see the hydraulic station configuration table for details); the hydraulic station adopts high and low pressure two-stage pressure; when the thin plate is punched, the double pump works at the same time, the speed is fast and the efficiency is high; when the thick plate is punched automatically Switch to high-voltage system; in standby standby state, the accumulator provides pressure, energy saving effect is good; equipped with servo proportional valve, controller, displacement sensor full-closed control, monitoring the position of the punch at all times, high control precision, can meet any stamping Process requirements. Ordinary cylinder type hydraulic station only has a single stage pressure, high pressure is used during stamping, the motor is fully loaded during standby, high energy consumption, serious damage to electrical and sealing components, and easy to cause oil leakage; ordinary hydraulic station is open loop design, only The stroke can be adjusted by the position switch, and only the stamping process can be performed, and the processing such as stretching cannot be performed.
(11) Automatic mold selection processing: The system can automatically select the most suitable mold to process. It can display the simulation of the processing track and path. If multiple parts are cut on the large plate, the plate can be saved to a large extent and the utilization of the material can be improved.
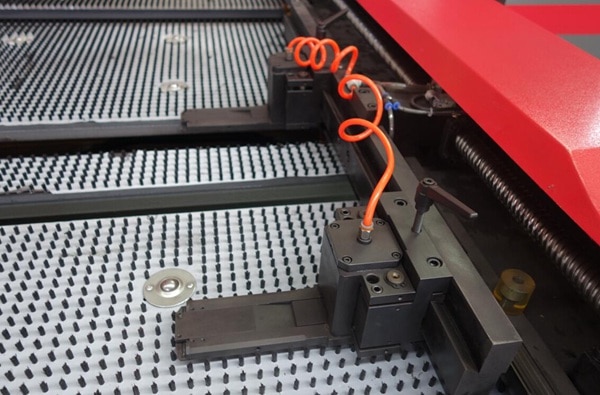
floating pneumatic clamps
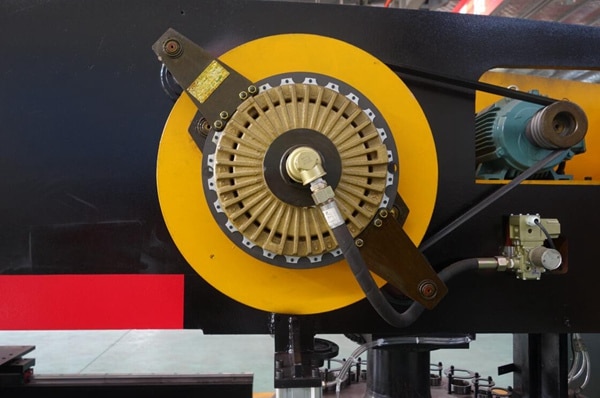
imported brand clutch

mold storage tooling
double guide rail
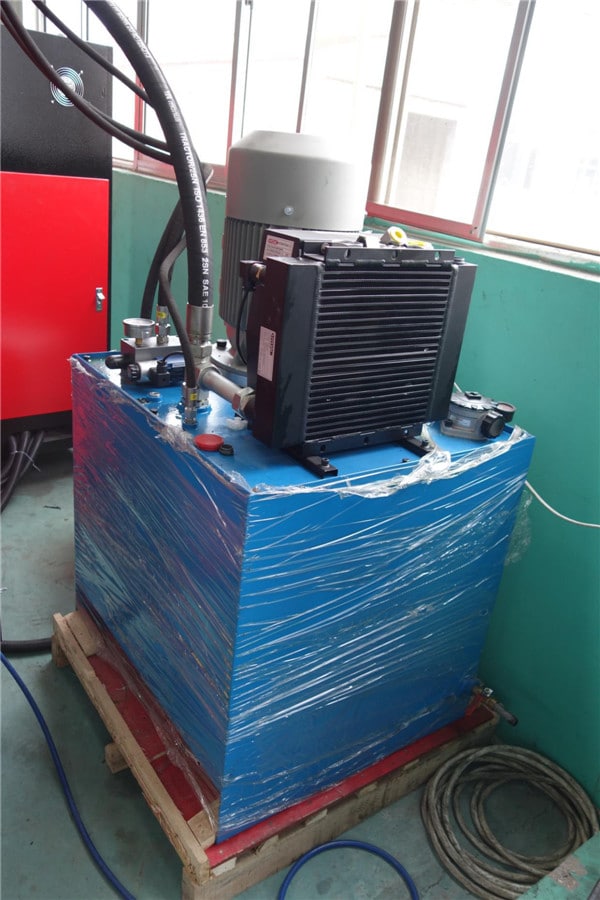
hydraulic station
(12) Rotary mold transfer station display, stamping time display, processing quantity display, mold life (punching times) display.
(13) The side of the fuselage is equipped with mold storage tooling to avoid mold damage caused by irregular placement of the mold, effectively protecting the mold, ensuring the stamping effect of the mold and prolonging the service life of the mold.